Manufacturing bolts is a critical segment of the fastener industry, encompassing an extraordinary blend of precision engineering and robust production capabilities. The process of bolt making captivates the industrial imagination, merging tradition with cutting-edge technology to deliver products that guarantee structural credibility and durability in varied applications.
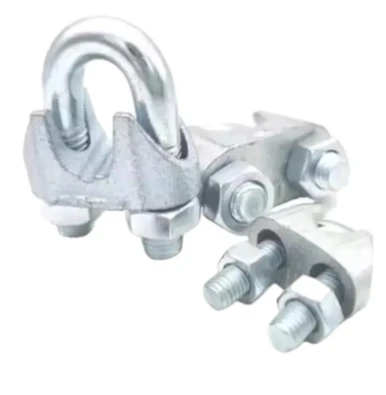
Bolts, although seemingly simple components, are omnipresent in construction, automotive, aerospace, and numerous other industries. These mechanical marvels secure some of the most vital structures and machinery in place, thanks to their meticulously engineered designs.
At the heart of bolt manufacturing is a highly systematic, multifaceted approach that begins with material selection. The choice of material, whether steel, titanium, brass, or alloy, directly correlates with the performance characteristics required of the final product. For example, high-strength steel bolts are preferred in construction due to their tensile strength and durability, whereas corrosion-resistant titanium might be selected for aerospace applications.
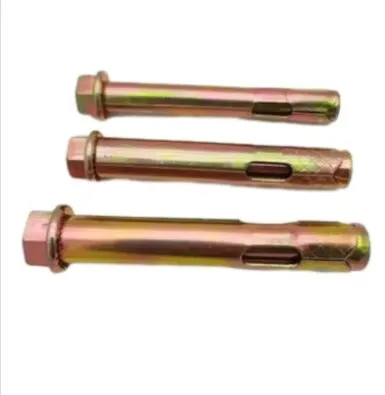
The journey from raw material to a finished bolt commences with wire drawing. This step involves pulling the wire through a series of dies to achieve the desired diameter while increasing its tensile strength. An emphasis on precision in this stage sets the tone for the manufacturing process, ensuring that the specifications are tailored accurately to industry standards.
Subsequently, the cold forging process transforms cut wire lengths into bolt blanks. This stage relies heavily on expertise and technological prowess, as it involves the application of immense pressure to form the head and body of the bolt without compromising its structural integrity. Advanced machinery equipped with programmable controls ensures that each bolt blank adheres to tight tolerances, a testament to the experience and authority of seasoned manufacturers.
Thread rolling follows, where the screw threads are impressed onto the blank through a rolling process. This method enhances the strength of the threads compared to traditional cutting or machining, ensuring reliability and performance under stress. The precision in threading not only affects the functionality but also the load distribution, playing a crucial role in how the bolt connects with its nut counterpart.
bolt making
Heat treatment and surface finishing are final stages that offer an added layer of reliability and longevity. Heat treatment imbues the bolt with enhanced mechanical properties such as higher strength and impact resistance, while surface treatments provide necessary corrosion resistance and aesthetic appeal. A deep understanding of metallurgical principles is fundamental to optimizing these phases, emphasizing the level of expertise and trustworthiness consumers expect from leading manufacturers.
Product testing is an indispensable component that underscores the quality and dependability inherent in bolt production. Rigorous tensile and shear tests, along with fatigue testing, underscore the manufacturer’s commitment to quality assurance, ensuring that each bolt can withstand its designed load and environmental exposures.
Trend advancements in bolt manufacturing are closely tied to technological innovation and sustainability concerns.
The integration of smart manufacturing and Industry 4.0 technologies, such as IoT and AI, is driving unprecedented levels of efficiency and customization. Moreover, the emphasis on environmentally friendly materials and processes is steering the industry towards a more sustainable future, reflecting the evolving priorities of consumers and stakeholders alike.
In addition to technological evolution, ongoing research and development deepen the industry's authority and adaptability to meet future demands. Strategic partnerships and collaborations with academic institutions bolster innovation, forging paths to discover new materials and processes that challenge the boundaries of traditional manufacturing norms.
In summary, bolt making is not merely a process of production; it is an intricate interplay of science, expertise, and technological acumen that drives quality and performance. Capturing the essence of Experience, Expertise, Authoritativeness, and Trustworthiness, manufacturers are not only crafting components but are securing the foundation upon which industries stand. As such, bolts remain an indispensable element, continuingly adapted to meet the diverse and intricate needs of modern engineering challenges.