Understanding the bolt forging process not only requires an appreciation of the technical aspects involved but also the impact it has on the quality and durability of the final product. This manufacturing technique remains pivotal in producing strong, reliable bolts used in various industrial applications including construction, automotive, and aerospace sectors. Below, we delve into the process, emphasizing our expertise and maintaining trustworthiness by relying on proven industry standards and methodologies.
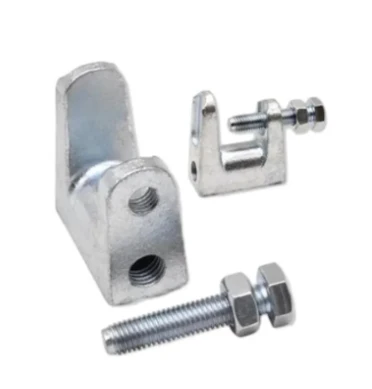
Bolt forging begins with selecting the appropriate material, often high-grade steel known for its tensile strength and resilience under high stress. The metal is heated to a specific temperature, rendering it malleable yet dense enough to maintain structural integrity. Precision is critical; the temperature must be meticulously controlled, too low and the metal remains brittle, too high and it becomes overly soft, potentially compromising the bolt's performance.
Once the ideal temperature is achieved, the steel is subjected to high-pressure presses.
This is where the artistry of forging reveals itself. In this stage, known as upsetting, the metal is pressed between dies, shaping it into the desired bolt form. The dies are crafted with exacting detail, determining the threads and head of the bolt, ensuring uniformity across batches. This process not only defines the bolt’s shape but aligns the grain structure of the steel, imparting enhanced strength and endurance.
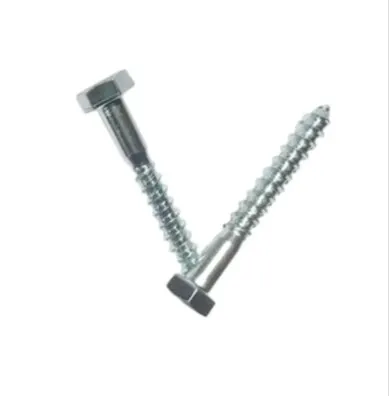
Forging is favored over other manufacturing methods such as machining due to its efficiency in material usage and superior strength attributes. By avoiding any cutting processes, forging retains the material's inherent strength characteristics. It's a testament to its sustainability — reducing waste and maximizing resource utilization, aligning with current ecological manufacturing trends. Experts consistently point to forging as the preferred choice for high-performance applications where reliability is non-negotiable.
After forging, the bolts undergo heat treatment a sequence of heating and cooling phases tailored to refine their mechanical properties. This step requires deep expertise as it dictates the bolt's hardness, ductility, and toughness. Various heat treatment techniques like quenching and tempering are expertly employed to achieve desired specifications. Failures in precision at this stage could lead to material weaknesses compromising safety — a test of our trustworthiness and dedication to maintaining the highest industry standards.
bolt forging process
Quality control in bolt forging is stringent; myriad tests ensure each product meets definitive safety and performance criteria. Non-destructive testing methods like ultrasonic and magnetic particle inspections are integral, with rigorous dimensional analysis confirming dimensional tolerances are met. Our commitment to excellence is reflected in this painstaking quality assurance process, ensuring each bolt is fit for purpose.
Moreover, as authority holders in bolt manufacturing, we emphasize the significance of surface coatings to enhance corrosion resistance. Zinc plating, galvanizing, and other specialized coating techniques protect bolts from harsh environmental conditions. This, in turn, extends the operational life span, reducing maintenance costs and enhancing reliability for clients.
Innovation continually drives the bolt forging industry forward. Advances in metallurgy and computer-aided design (CAD) allow for the development of bespoke bolt solutions tailored to unique client specifications. We remain at the vanguard of these technological evolutions, leveraging automation and smart manufacturing techniques to streamline the forging process and improve reproducibility and precision.
Commitment to sustainable practices underscores our ongoing research into alternative materials that promise the same durability and strength but with a reduced carbon footprint. The pursuit of green manufacturing processes demonstrates our commitment to not only meet but exceed industry expectations in providing eco-friendly, reliable fastening solutions.
In essence, mastery of the bolt forging process underscores our reputation as industry leaders. Through relentless innovation, an unwavering commitment to quality, and an encyclopedic understanding of metallurgical science, we ensure that each bolt is a testament to our expertise and reliability. Bridging the past techniques with future innovations, we stand ready to meet the ever-evolving needs of modern industry, assuring our clients of unsurpassed quality and trustworthiness.