In a world where ensuring the smooth and efficient functioning of mechanical systems is key, bolt operation becomes a critical factor in product maintenance and assembly. Industry experts often stress the importance of this seemingly simple process, which plays a vital role across various sectors, from automotive to construction. Understanding bolt operation goes beyond basic knowledge; it's about mastering an art that can save time, ensure safety, and prevent future mechanical failures.
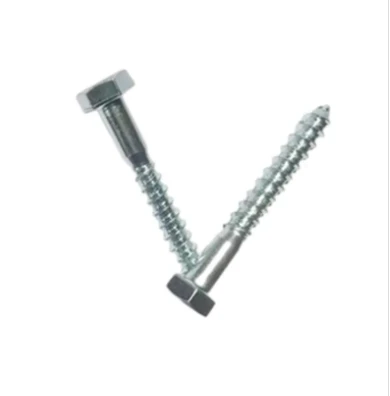
Professional experience reveals that a robust bolt operation strategy hinges upon selecting the correct type of bolt for specific applications. Not all bolts are created equal, and choosing the wrong one can compromise the integrity of the entire structure or mechanism. For instance, high-strength bolts are appropriate for heavy-duty applications such as bridges and skyscrapers, where sturdiness and reliability are paramount. Conversely, lighter applications may only require standard-grade or even customized bolts designed for particular circumstances.
In bolted joint assembly, torque is a term often associated with bolt operation. Experts emphasize that applying the correct torque is not just beneficial but essential. Proper torque ensures that flanges and other components are sufficiently secured without being excessively tightened, which can cause strip threading or bolt failure. Those in machining and engineering roles understand that utilizing a calibrated torque wrench is vital for precision in bolt operation, ensuring that every bolt fulfills its intended purpose without causing undue stress on the surrounding materials.
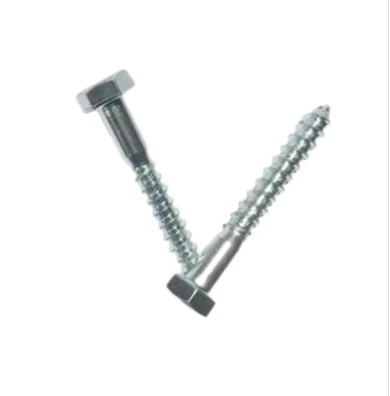
When discussing bolt operation, threading compatibility cannot be overlooked.
Misalignment can lead to significant malfunctions or degrade the operational efficiency of the equipment. Therefore, specialists advocate for meticulous alignment checks during installation, which involve verifying that bolt threads match the nut threads perfectly. Using lubricants can also ease the installation process, reducing wear and tear on the bolt itself while facilitating a more secure fit.
bolt operation
Reliability in bolt operation also involves routine inspections and maintenance - not aspects to be perceived as optional. Regular checks for signs of wear, fatigue, or corrosion in bolted joints can preempt costly repairs and extend the lifecycle of machinery. In particularly harsh environments, such as marine or chemical processing industries, bolts are subject to factors that may accelerate their degradation. Here, implementing a proactive maintenance schedule informed by experience and expertise maximizes the functionality of the entire assembly and minimizes risks.
The innovative use of technology in bolt operation further underscores its critical role. More companies are investing in smart technologies like digital torque wrenches and inspection cameras that provide real-time data and insights instantly. These advancements signify more than just technological progress; they reflect a shift towards more informed approaches that prioritize precision and efficiency in bolt operations.
The industry-specific standards and certifications add another layer of trustworthiness to bolt operation. For businesses, adhering to such standards ensures compliance with international benchmarks, enhancing credibility with clients and regulators alike. This adherence is crucial where bolt operation directly impacts safety—a factor emphasized by industry authorities who advocate for following standardized procedures.
Ultimately, the meticulous understanding and application of bolt operation transcend basic mechanic functions. It is about ensuring safety, enhancing performance, and achieving the high standards expected in modern engineering practices. By cultivating expertise and leveraging technological advancements, professionals in the field can execute bolt operations confidently while enhancing the structural integrity of their projects, ushering in an era of reliability and excellence.