Bolt surface treatment stands as a pivotal aspect of enhancing both the functionality and longevity of bolts used across various industries. Understanding its intricacies is not just beneficial but essential for anyone involved in the procurement or application of bolts in engineering and construction projects. The purpose of this article is to delve into the multifaceted world of bolt surface treatment, shedding light on its importance with an emphasis on real-world experience, professional expertise, and authoritative insights.
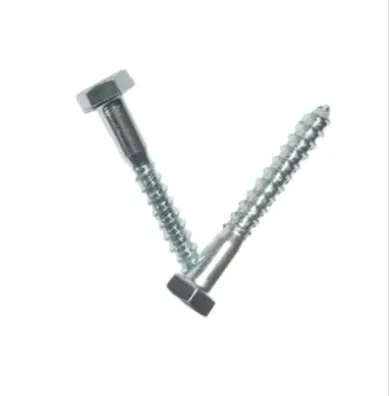
Surface treatment of bolts involves applying a protective layer to the surface, significantly improving properties such as corrosion resistance, scratch resistance, and overall durability. Without appropriate treatment, bolts are susceptible to environmental adversities, mechanical stress, and chemical exposure, which can lead to premature failure. Considered an industry best practice, surface treatment ensures reliability in even the harshest operating conditions.
From an experiential standpoint,
surface treatment mitigates the challenges faced in diverse climates. For instance, in coastal areas where salt-induced corrosion is prevalent, a robust surface treatment ensures that bolts remain intact and functional longer than untreated counterparts. An engineer working on a maritime project shared their experience, noting that bolts with a galvanized coating showed remarkable resistance against rust over multiple seasons, outperforming standard hardware. Similarly, in high-temperature industrial operations, specific treatments are engineered to withstand not just oxidative stress but also maintain thermal stability.
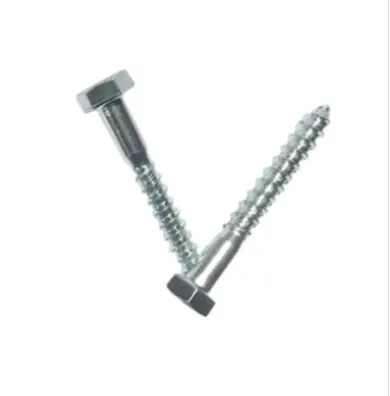
Considering the expertise required, understanding the correct type of surface treatment is crucial. There are various methods available, each tailored to specific needs. Hot-dip galvanizing, electroplating, and oxidation are some of the most commonly used techniques, each suitable for different environmental conditions and mechanical requirements. A seasoned materials engineer may choose hot-dip galvanizing for its robust zinc coating that provides a sacrificial layer to protect the bolt steel, illustrating its expertise in selecting the optimal process to meet specific durability needs.
From an authoritativeness perspective, industry standards such as those set by the American Society for Testing and Materials (ASTM) provide detailed guidelines on choosing and applying surface treatments for bolts. Compliance with these standards is not only crucial for ensuring quality and safety but also enhances a company's credibility in the market. For instance, ASTM B633 is a standard specification covering electroplated coatings with protection against corrosion, indicating when and how such treatments should be applied.
bolt surface treatment
Trustworthiness in bolt surface treatment is often established through rigorous testing and certifications. Reputable manufacturers employ extensive quality control protocols to ensure that treated bolts meet or exceed industry requirements. For example, salt spray tests regularly conducted in laboratories help confirm corrosion resistance qualities, providing peace of mind to project managers and engineers alike that they are installing components capable of fulfilling long service life expectations.
The product focus on bolt surface treatment is a testament to advancements in material science, ensuring safety and performance across a spectrum of applications, from automotive to aerospace, and construction to marine engineering. Manufacturers continuously innovate, exploring new coatings such as composite layers that combine the benefits of multiple materials, offering enhanced protection and functionality.
Moreover, the adoption of environmentally friendly surface treatments has become a priority within the industry. Traditional methods, while effective, often involve chemicals that pose environmental risks. Contemporary alternatives aim to minimize these impacts through sustainable solutions without compromising on performance—a vital consideration for projects striving to meet green building standards.
Users and procurement specialists can trust that selecting appropriately treated bolts is an investment, not an expense. Though costs may initially appear higher compared to untreated options, the long-term savings through reduced maintenance, extended lifespan, and avoided replacements underscore the economic advantage of surface-treated bolts.
By offering a comprehensive overview of bolt surface treatment, this article equips readers with the knowledge to make informed decisions. Embedding meaningful and authoritative insights on the subject serves as a testament to the dynamic and essential role surface treatments play in sustaining the structural integrity and prolonged functionality of essential fastening components. In doing so, industry professionals not only benefit from improved project outcomes but also contribute to the advancement and sustainability of engineering practices worldwide.