The process of bolt making is a fascinating blend of traditional craftsmanship and modern manufacturing techniques that are essential in a myriad of industries, from construction to automotive engineering. With growing demand for robust and reliable fasteners, understanding the steps involved in creating high-quality bolts is crucial for businesses and engineering professionals. This comprehensive overview offers insights into the bolt making process, focusing on practical experiences, expert techniques, and authoritative practices.
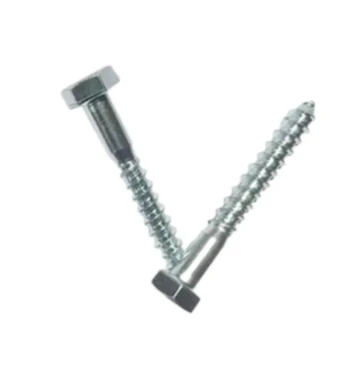
Manufacturing Process Overview
The bolt making journey begins with selecting the appropriate raw material. Typically, manufacturers choose between carbon steel, alloy steel, stainless steel, or brass depending on the intended application, required strength, and environmental considerations. The selected metal is ordered in large quantities to ensure consistency and quality throughout production, showing dedication to material reliability.
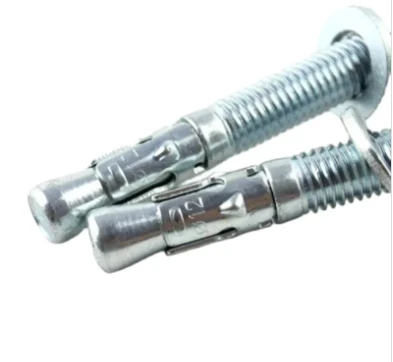
Cutting and Shaping Raw Material
Next in line is the cutting phase, where the raw material is shaped into uniform rods. This step involves meticulous precision to ensure that each rod matches specific dimensions. Automated cutting machines equipped with high-precision blades are employed to achieve these exacting standards. This stage demonstrates expertise in handling raw materials and integrating technology to increase efficiency.
Forging – The Backbone of Bolt Strength
Forging is arguably the most critical step in bolt making. It not only determines the strength and durability of the finished bolt but also introduces the thread structure that is crucial for its functionality. The rods are heated to a specific temperature that makes the metal malleable without losing its innate strength. Controlled deformation techniques are applied using dies and presses, forming the bolt’s head and body.
This forging process underscores the importance of technical proficiency, combining traditional methods with cutting-edge machinery to uphold the highest standards of quality. Experienced workers adjust the temperature and pressure to ensure each batch maintains the desired characteristics, further reinforcing expertise.
Thread Rolling Precision and Consistency
After the forging process, threads are added to the bolt shaft, a defining feature crucial for fastening. Instead of cutting, threads are generally rolled onto the bolt. This cold-forming technique enhances the mechanical properties of the bolt, such as tensile strength and fatigue resistance. Rolling also improves surface finish and precision, which are vital for a secure fit in different applications.
Operators skilled in adjusting thread rolling machines ensure consistency across large production runs, demonstrating a commitment to precision engineering and expertise developed through years of hands-on experience.
bolt making process
Heat Treatment Optimizing Mechanical Properties
To maximize strength and resilience, bolts undergo a carefully controlled heat treatment process. Depending on the material and application requirements, processes such as quenching and tempering are used to adjust hardness and flexibility. Such treatments are critical for bolts intended for high-stress environments, where failure is not an option.
Manufacturers employ top-tier engineers who meticulously program furnace cycles to achieve desired mechanical properties, highlighting the authoritative expertise required in this field. This attention to detail ensures that the bolts meet international safety and quality standards, fostering trust among users.
Coating and Surface Finishing
Post-treatment, bolts often require protective coatings to enhance their resistance to corrosion and wear. Common methods include galvanization, plating, or adding a coating of protective paint. These coatings not only protect the bolt in adverse conditions but also contribute to its aesthetic appeal.
At this stage, manufacturers exhibit their authority on product longevity and appearance by selecting appropriate coatings tailored to specific environments and customer needs. This strategic decision-making reflects trustworthiness, as manufacturers prioritize customer satisfaction and long-term performance.
Quality Control Measures
The final step in the bolt making process is thorough quality control.
Each bolt undergoes rigorous testing procedures to ensure compliance with industry standards. Tests include tensile strength checks, dimension accuracy verifications, and surface quality assessments. Employing cutting-edge technology and experienced inspectors, manufacturers ensure that only those bolts meeting strict criteria reach the market.
Reliable quality control reinforces the trustworthiness of bolt manufacturers, guaranteeing that every product delivers on its promised specifications. By investing in comprehensive testing, companies solidify their position as leaders committed to providing dependable fastening solutions.
Concluding Remarks
The bolt making process is an intricate blend of experience, expertise, authority, and trustworthiness, shaping products that hold structures together and ensure safety across multiple sectors. Those involved in bolt manufacturing continuously refine their processes, adhering to high standards that satisfy both current demands and future innovations in engineering and construction. This dedication to quality and precision bolsters both user confidence and the manufacturer's reputation in a competitive global market.