Hollo bolts have revolutionized the construction and metalwork industries due to their unique ability to create secure connections within hollow sections, offering a viable solution where conventional bolts won't suffice. Understanding the different hole sizes for hollo bolt installation is essential for maximizing their performance, ensuring safety, and guaranteeing structural integrity.
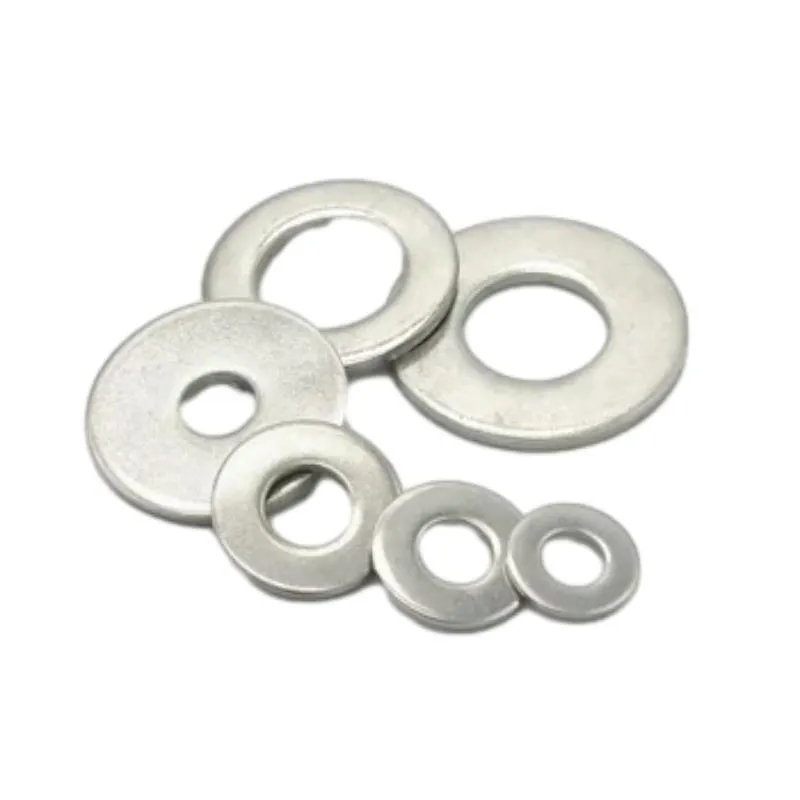
The selection of appropriate hollo bolt hole sizes is critical and varies depending on multiple factors, including bolt size, material type, and the specific requirements of the project. In general, the size of the hole is determined by the bolt's diameter, which ensures the bolt fits securely without unnecessary slack that might compromise stability. For instance, for an M12-size hollo bolt, the hole dimension would typically be around 14mm to provide a snug fit that allows for easy insertion without compromising grip strength.
Professionals with extensive experience in hollo bolt applications emphasize the importance of precision when drilling holes for these bolts. A deviation as small as a millimeter can impact the load-bearing capacity of the bolt, ultimately affecting the safety of the entire structure. This precision requires expert drilling techniques and often the utilization of high-quality industrial drills.
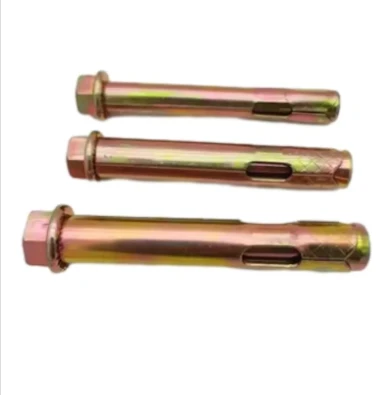
Expertise in material science contributes significantly to understanding how different substrates affect the choice of hollo bolt hole sizes. Steel, being one of the most common materials utilized with hollo bolts, demands a certain degree of understanding of its expansion and flexibility properties. An authoritative approach can help in selecting the correct drill bit and ensuring that the hole's size remains constant and within specified tolerances despite metal's tendency to warp or expand.
hollo bolt hole sizes
Authoritative sources in the construction industry recommend adhering strictly to manufacturer specifications for hole sizes in hollow sections. These guidelines are developed from rigorous testing and engineering principles, ensuring that the hollo bolts can perform optimally under specific load conditions. Knowledge of standards, such as those set out by the American Institute of Steel Construction (AISC) or European Committee for Standardization (CEN), can reinforce trust in the structural adequacy of projects utilizing hollo bolts.
Trustworthiness in hollo bolt applications extends to ensuring quality control in both the production and installation phases. This includes verification of specifications such as tensile strength and load tolerances, often documented in quality assurance reports. It also involves ensuring that the drilling process; including hole size calibration, is supervised by experienced professionals who can preemptively address any issues that might arise.
Case studies further illustrate the success of properly installed hollo bolts, revealing how projects ranging from high-rise buildings to complex architectural designs have benefitted from the reliability of these fasteners when used correctly. Professionals share their experiences and practical knowledge in industry forums, contributing to a growing understanding and authoritative guidance on best practices for hollo bolt applications.
In conclusion, the selection of appropriate hollo bolt hole sizes is integral to achieving a reliable and secure connection within hollow sections. By prioritizing expertise in drilling techniques, adhering to authoritative standards, and committing to trustworthy installation practices, professionals can ensure the safety and efficiency of structures that employ hollo bolts.