Choosing the right type of bolt for any project is crucial for ensuring integrity, durability, and safety. Bolts, often an overlooked component, play an indispensable role in construction, manufacturing, automotive, and various other industries. The plethora of bolt types can be overwhelming, yet understanding them is crucial for optimizing any project's success. This comprehensive guide will delve into the various types of bolts, emphasizing their applicability, strengths, and potential limitations, all essential factors for informed decision-making.
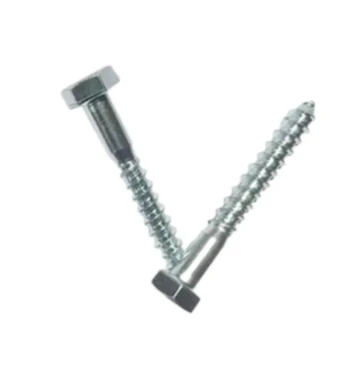
Hex bolts, one of the most common types, are well-known for their versatility. These bolts feature a six-sided head, typically used in conjunction with a nut or tapped hole. Their design facilitates wrench access from various angles, making them ideal for numerous applications. Hex bolts are often utilized in the construction of bridges, buildings, and machinery. Their strength and durability make them suitable for projects that endure significant stress. However, choosing the right material—be it stainless steel, zinc-plated steel, or alloys—is vital for ensuring resistance to corrosion and suitability for the intended environment.
Carriage bolts, identified by their round, smooth head and a square neck, are primarily used in wood applications. The unique design prevents rotation during tightening, which is a critical feature when securing wood. Carriage bolts are frequently used in deck construction due to their ability to hold wood firmly without causing damage or splitting. However, these bolts are not ideal for applications requiring frequent disassembly, as their design makes removal more challenging without specialized tools.
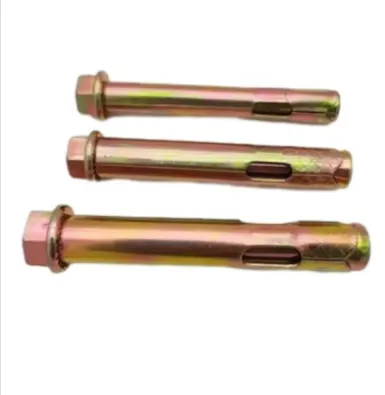
Lag bolts, akin to large screws, are designed for demanding applications. Their robust threads facilitate firm embedding into wood or plastic. Often used in heavy construction, lag bolts are invaluable for projects requiring strong bonding and high load-bearing capabilities, such as in the assembly of playground equipment or fastening large wooden beams. Selecting lag bolts made from weather-resistant materials ensures the longevity and reliability of outdoor installations. However,
users should be mindful of pre-drilling holes to prevent wood splitting.
Another essential category is the machine bolt, featuring a flat or hex head with a threadless shank. Designed explicitly for metal-to-metal and metal-to-wood applications, machine bolts are indispensable in automotive and heavy machinery industries. Their role in securing critical mechanical parts underlines the importance of precision in choosing both bolt grade and material. Stainless steel and alloy variants offer enhanced durability, crucial for enduring high temperatures and corrosion.
all kinds of bolts
Flange bolts stand apart with their built-in washers beneath the head, distributing load evenly across a surface. This unique design makes flange bolts ideal for bolting softer materials where load distribution is crucial, as found in plumbing and electrical assembly. Their increased surface area minimizes the risk of damage and ensures a more secure fastening. However, it is important to ensure the surface finish aligns with project demands, especially in aesthetic-sensitive applications.
Eye bolts serve as an excellent solution for lifting and load-bearing tasks. Their circular, closed loop at one end provides a reliable point for slings and ropes, aiding in the transportation of heavy materials and equipment. Available in various sizes and load ratings, ensuring the proper selection of eye bolts is critical for safety in engineering and rigging applications. While eye bolts are generally robust, consistent inspection for wear and stress indicators is crucial in maintaining operational safety.
For projects requiring rapid assembly and dismantling, shoulder bolts serve as the go-to option. Also known as stripper bolts, these fasteners have an unthreaded shoulder, allowing for rotational or sliding movement of attached parts. They're extensively used in mechanical and automotive industries for applications like engines and pulleys. The choice of shoulder bolt material can drastically affect performance, with stainless steel providing superior resistance to wear while bearing loads.
In conclusion, the right bolt selection simplifies project execution, enhancing both safety and effectiveness. Understanding each bolt's unique applications, strengths, and potential downsides ensures the right fit for specific project requirements. Utilizing bolts crafted from suitable materials and designed for specific applications is fundamental, whether safeguarding a structure or ensuring the longevity of an automotive component. Trusting expert recommendations and staying informed on the latest advancements in bolt technology can significantly enhance any project's outcomes.