Anchor fastener fittings represent a crucial component in construction and various industrial applications due to their ability to secure structures reliably. Over the years, these fittings have evolved significantly, reflecting advancements in engineering and materials science. As industries continue to demand higher performance and durability from their fastening solutions, understanding the nuances of anchor fastener fittings becomes paramount for both users and specifiers.
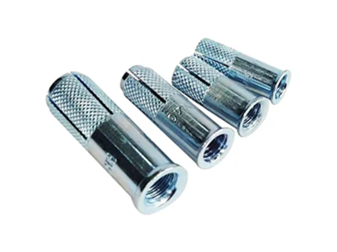
When selecting an anchor fastener fitting, one must consider the environment in which it will be used. Different environments pose varying challenges, from corrosion in marine contexts to temperature fluctuations in industrial settings. Stainless steel and high-strength alloys are often chosen for their resistance to environmental stressors. Opting for the right material not only ensures the longevity of the fittings but also enhances the safety of the entire structure they support.
The design of anchor fastener fittings is another critical aspect that cannot be overlooked. While traditional designs have served basic needs, modern requirements push for innovative solutions that accommodate greater loads and provide easier installation. For example, some contemporary designs incorporate self-locking mechanisms that prevent loosening under dynamic loads. This innovation is particularly beneficial in applications where vibrations are a concern, such as in automotive or aerospace industries.
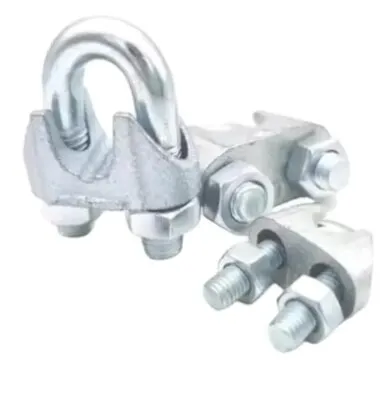
Performance is directly influenced by the fastening technique employed. Mechanical anchors, for instance, rely on friction and mechanical interlock with the substrate, making them ideal for concrete and masonry. In contrast, chemical anchors use adhesive compounds to bond the fitting to the substrate, offering superior load distribution and flexibility. Professionals recommend assessing the substrate material for compatibility before deciding on a type. Adhering to installation guidelines provided by manufacturers is essential to harness the full potential of these fittings.
It's imperative to verify the load ratings and testing certifications of anchor fastener fittings. Reputable manufacturers will provide detailed documentation, including testing results according to international standards such as ASTM or ISO guidelines. These certifications not only verify the product's capability but also build trust with the user, knowing they are investing in a proven solution. Structures with high safety requirements, like skyscrapers or bridges, mandate rigorous testing and often necessitate third-party verification to ensure compliance with safety norms.
anchor fastener fitting
The expertise required in choosing the right anchor fastener fitting extends beyond technical specifications to include an understanding of legal and safety regulations.
Various regions have specific codes that dictate the type and installation methods of anchor fasteners in construction. For instance, earthquake-prone areas may have stringent requirements to ensure that structures can withstand seismic activities. Consulting with a structural engineer or a specialist familiar with these regulations can help avoid costly mistakes and ensure compliance.
Training and experience are vital for those involved in the installation of anchor fastener fittings. A comprehensive understanding of tools, techniques, and safety protocols minimizes the risk of improper installation, which could lead to structural failures. Training programs offered by manufacturers or independent organizations provide valuable hands-on experience, helping installers keep abreast of the latest developments and best practices in the field.
The choice of supplier or manufacturer also plays a significant role in the successful implementation of anchor fastener fittings. Working with a reputable supplier that offers comprehensive support, including technical advice, installation training, and after-sales service, enhances the user experience. Suppliers who invest in research and development contribute to the advancement of fastening technologies, providing users with cutting-edge solutions that meet modern demands.
Finally, customer reviews and case studies provide practical insights into the real-world performance of anchor fastener fittings. Learning from the experiences of other users can uncover potential challenges and highlight strengths not immediately apparent from technical specifications alone. This shared knowledge serves as an invaluable resource for both novice and seasoned users seeking to optimize their fastening projects.
In conclusion, the realm of anchor fastener fittings is complex, requiring a blend of technical knowledge, practical experience, and understanding of regulatory requirements. By focusing on the pivotal aspects of material selection, design innovation, installation techniques, and supplier credibility, users can make informed decisions that ensure the safety and durability of their structures. As the industry evolves, staying informed about the latest advancements and trends will remain crucial for those aiming to achieve superior outcomes with their fastening solutions.