Bolt heads come in a diverse array of types, each engineered to meet specific needs across various industries. Understanding these variations is crucial for ensuring optimal performance, structural integrity, and safety. While bolts may seem like simple components, their design nuances can carry significant implications.
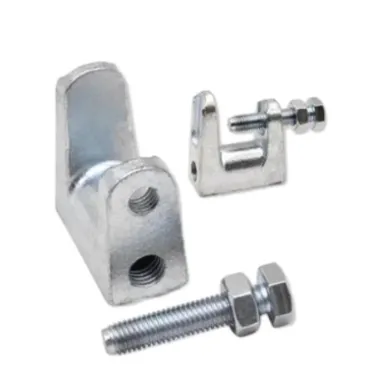
One of the most common bolt head types is the hex head bolt. Recognized for its six-sided structure, this design allows for easy gripping from multiple angles. Hex head bolts are widely used in construction, manufacturing, and automotive industries due to their versatility. They are especially favored in mechanical settings where tightening and loosening must occur with precision and ease.
Another popular choice is the square head bolt. With four flat sides, this design provides broad contact surfaces for wrenches, ensuring a firm grip even under high torque. Historically, square head bolts were more commonly used during the industrial revolution, and they still have applications in restoration work and scenarios where a rustic appearance is desired.
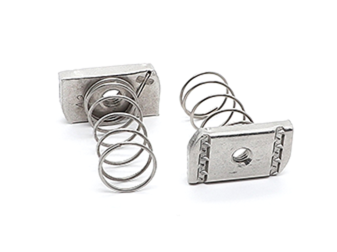
The round head bolt, characterized by a smooth, dome-shaped head, is often employed in applications where aesthetics matter just as much as functionality. Its design helps in preventing scratches and injuries, making it ideal for furniture assembly and other consumer products where surface smoothness is a concern.
Carriage bolts are distinguished by their rounded heads and a square neck under the head. This design is strategic, as the square neck prevents the bolt from turning when secured in a square hole, a feature that proves advantageous in woodworking and assembly jobs where ease of installation and a flush finish are priorities.
Flat head bolts, otherwise known as countersunk bolts, are particularly suited for applications requiring a flush surface. As the name suggests, the head of this bolt is designed to sit flush with or below the surface material, making them indispensable in woodworking, metalwork, and other industries where streamlined surfaces are essential.
Eye bolts feature a forged circular head that forms a loop, and they are predominantly used for lifting, rigging, and anchoring applications. The eye provides an attachment point for ropes or cables. Selecting the right eye bolt is critical, as improper use or installation can lead to catastrophic failures, especially in weight-bearing applications.
bolt head types
Another key variant is the T-head bolt, which has a T-shaped head designed to fit into slots and channels. T-head bolts are frequently used in machine tool environments and in the construction of assembled products where other fastening elements may be unfeasible due to space constraints.
For environments where security is paramount, such as public infrastructure or secure facilities, tamper-proof bolts with uniquely patterned heads, such as pin-head or snake eye, are utilized. These bolts afford an additional layer of security, as they require specific tools for installation and removal, thus reducing the risk of theft or tampering.
Specialty bolts like the flange bolt integrate a washer-like surface, which distributes a load more evenly. This design is advantageous in bolted connections where material strength and distribution of force are critical, such as in automotive undercarriage assemblies.
While understanding these different bolt head types is vital, selecting the suitable material and coating also plays a decisive role in bolt performance. Stainless steel is favored for its rust resistance and durability, while galvanized coatings provide corrosion protection in harsher environments. In certain applications, such as electronics or sensitive assemblies, non-metallic materials like nylon may be used to prevent electrical conduction and reduce weight.
Certification and testing offer an indication of a bolt's quality and compliance with industry standards such as ANSI, ISO, or DIN. Ensuring that your bolts adhere to these specifications is not just about meeting regulatory requirements; it is about ensuring safety and longevity in your structures or products.
The expertise required to select the appropriate bolt head encompasses understanding load ratings, materials science, and the mechanics of fastening. Consulting with professionals and leveraging technological tools like CAD design can save time, reduce costs, and mitigate risks associated with improper bolt selection.
Building trust and authority in bolt selection and application extends to following proper documentation processes, validating credentials, and providing transparent information about the bolt's life cycle. In an industry where precision and reliability can define success, the integrity of your fastening components should never be compromised. With the right choice of bolt head types, combined with expert advice and quality assurance, your projects are primed for safety, efficiency, and success.