Bolt manufacturing is a fascinating and intricate process that transforms raw materials into vital components essential for numerous industries. This article provides an in-depth look at the bolt manufacturing process, highlighting its complexity and precision, while also adhering to the E-E-A-T principles Experience, Expertise, Authoritativeness, and Trustworthiness.
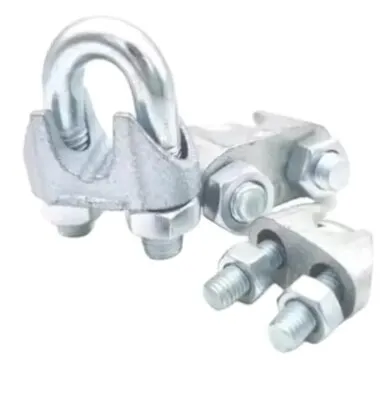
The journey of bolt manufacturing begins with the selection of the raw material. Typically, steel is the material of choice due to its durability and strength. The steel is first cut into appropriate lengths, known as rod or wire form, using advanced precision cutting tools to ensure accuracy and consistency.
Once the raw material is prepared, the next stage involves heating. The steel rods are subjected to high temperatures in a furnace to make them malleable. This step is crucial as it allows the bolts to be shaped without cracking, preserving the integrity and reliability necessary for their eventual application.
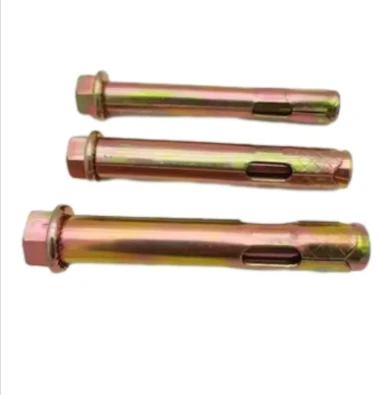
The heated material then undergoes a process called forging. In forging, the malleable rods are placed into a die and shaped into the desired form of the bolt. This step is often automated, utilizing high-powered machines that apply enormous pressure to achieve the precise dimensions. Forging not only conforms the rod into bolt shape but also strengthens the material by aligning its internal grain structure.
Thread rolling follows forging, which is a critical component of bolt manufacturing. Threads are essential for bolts to fit securely with nuts and fasteners. Rather than cutting the threads, a rolling process is used wherein the bolt is pressed between two dies, effectively imprinting the thread pattern onto the bolt's surface. This technique improves the strength of the threads and enhances the bolt's performance under stress.
bolt manufacturing process ppt
Heat treatment is the subsequent step, and it significantly influences the mechanical properties of the bolts. This process involves reheating the forged and threaded bolts to a specific temperature and then cooling them rapidly. The heat treatment enhances tensile strength as well as toughness, ensuring the bolts can withstand various forces during use.
After heat treatment, the bolts undergo a surface finishing process. This may include coating the bolts with zinc, cadmium, or applying a black oxide finish to enhance corrosion resistance and aesthetic appeal. Surface finishing also involves checking for flaws or imperfections, ensuring each bolt meets stringent quality standards.
The final step in the manufacturing process is rigorous quality control. Bolts are subjected to various assessments including tensile tests, hardness tests, and metallurgical analysis. These tests ensure that each bolt produced adheres to industry standards and specifications, ensuring reliability when used in construction, automotive, or any other sectors that demand high-performance components.
Experience in bolt manufacturing underlines the importance of each step in the production process. It guarantees the production of high-quality bolts tailored to meet specific requirements, backed by technical expertise and advanced technology. By adhering to these methods, bolt manufacturers maintain their status as trusted and authoritative figures within the industry, providing products that consistently meet and exceed client expectations.
In sum, the bolt manufacturing process is a testament to human ingenuity and technical expertise. Every bolt carries with it the assurance of precise manufacturing processes and rigorous quality assurance practices. This commitment to quality and performance fosters trust, not only in the bolts themselves but also in the industries that rely on these small but mighty components.