The modern bolt production process is a sophisticated journey that blends age-old craftsmanship with cutting-edge technology, ensuring a steady output of quality fasteners. At its core, bolt production is not merely about churning out products but involves a meticulous series of steps that guarantee strength, reliability, and precision.
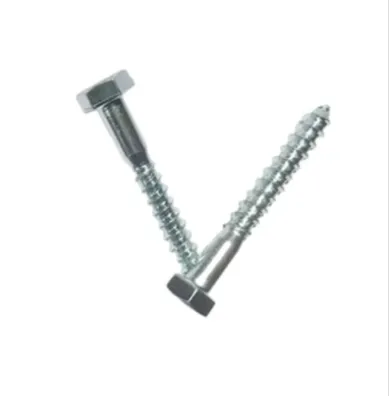
The journey begins with raw materials, primarily high-grade steel wire, which serves as the backbone of a durable bolt. This steel wire is subject to a stringent selection process, ensuring only the best quality material is used. The wire is meticulously cleaned to remove any residual impurities that could compromise the integrity of the finished product. This cleaning process, often called pickling, involves chemical baths that prepare the wire for further handling.
Once cleaned, the wire undergoes cold forging, a pivotal step where it takes on its initial bolt shape. Cold forging involves subjecting the wire to high pressure in dies and tools, effectively forming the bolt head and shank without the need for heat, thereby preserving the material’s inherent strength. This process is revered for enhancing the bolt's metallurgical properties, ensuring exceptional durability and load-bearing capacity.
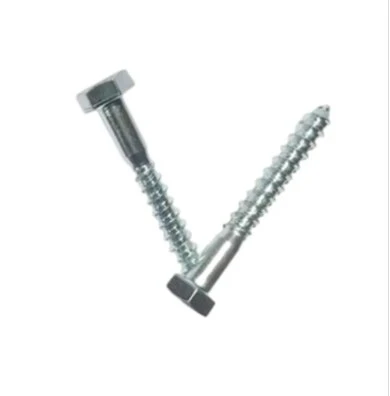
Threading is the next crucial phase. Using either rolling or cutting techniques, the bolt gains its distinctive threads. Thread rolling is a preferred method due to its ability to maintain the material's grain structure and increase tensile and shear strength. During this stage,
precision is paramount. Any deviation can result in performance issues or failure in application, making the expertise of the technicians and the quality of the threading equipment vital.
bolt production process
Following threading, bolts are heat-treated to enhance hardness and mechanical properties. Heat treatment involves controlled heating and cooling cycles that modify the bolt's internal structure, fine-tuning its strength and flexibility to withstand various demanding conditions.
With the mechanical properties set, the bolts move to the surface finishing stage. This is not just about aesthetics, though it does give the bolts a polished look. Coatings such as zinc, cadmium, or phosphate are applied to improve corrosion resistance, a crucial factor in extending the lifetime of bolts used in harsh environments.
Throughout these stages, rigorous quality control measures are employed to ensure each bolt meets strict industry standards. From tensile tests to microscopic examinations, every bolt is scrutinized to confirm its dimensions, strength, and durability. This commitment to quality speaks to the expert knowledge and authoritative standards embedded within the production process.
What sets this process apart in the industry is not just the technical precision but the trustworthiness cultivated through consistent quality. Manufacturers have honed this procedure to embody both expertise and reliability, ensuring every bolt rolling off the production line is a testament to decades of technological advancement and craftsmanship. This comprehensive understanding of the bolt production process highlights a commitment to excellence, underscored by a dedication to producing fasteners that perform flawlessly in every application, earning the confidence of industries worldwide.