Achieving top-tier bolt quality is paramount in ensuring the safety and efficiency of countless applications across various industries. Understanding what defines superior bolt quality involves a deep dive into materials, manufacturing processes, and performance standards that continually evolve to meet the stringent demands of modern engineering. Here's a comprehensive exploration of the critical factors contributing to bolt quality, with insights geared towards establishing your authority in the field.
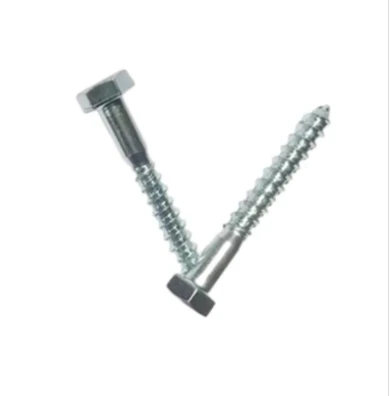
Firstly, material selection is a cornerstone of bolt quality. High-quality bolts are typically made from materials that offer a superior balance of strength, ductility, and corrosion resistance. Common materials include alloy steel, stainless steel, and, for more specialized applications, titanium and Inconel. Each material has unique properties that make it suitable for specific environments and loads, underscoring the importance of choosing materials wisely based on the intended application.
Beyond materials, the manufacturing process plays a vital role in bolt quality. Precision in manufacturing ensures that bolts are made to exact specifications, minimizing variability and potential failure points. Advanced manufacturing techniques such as cold forging and hot forging are employed to enhance the mechanical properties of bolts, providing a fine grain structure that leads to improved fatigue resistance. Moreover, post-processing treatments like heat treatment and surface finishing are crucial in enhancing bolt strength and longevity. It is essential to ensure that manufacturing facilities adhere to strict quality control protocols at every stage, from material selection to final inspection.
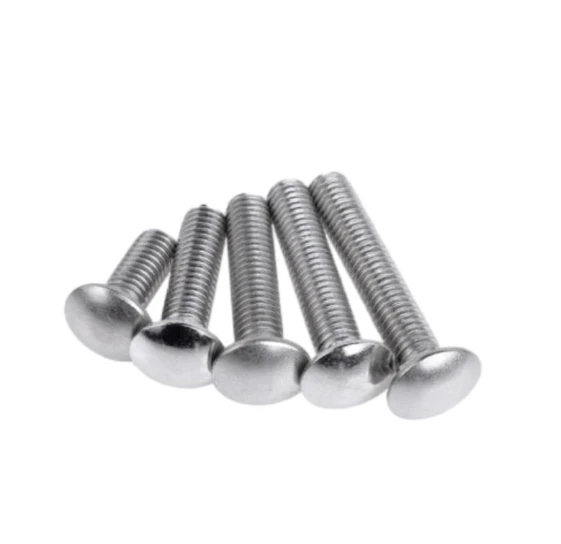
In terms of performance standards, adherence to international standards such as ISO, DIN, and ASTM ensures that bolts meet globally recognized benchmarks for quality and safety. However,
innovation doesn't stop at compliance. Leading manufacturers often exceed standard requirements by implementing rigorous in-house testing procedures. These include tensile testing, fatigue testing, and non-destructive testing methods like ultrasonic and magnetic particle inspection, which help in detecting potential defects before the bolts reach the market.
bolt quality
Another key aspect of bolt quality revolves around innovative design and engineering. Bolts are increasingly being engineered for specific applications with unique geometries and features that enhance their performance. For instance, some bolts are designed with self-locking capabilities to prevent loosening under vibration, while others may feature coatings that provide enhanced environmental resistance. Such innovations require a high level of expertise and a thorough understanding of the stresses and conditions the bolts will endure in their lifecycle.
Bolts, being critical components in construction and manufacturing, must also instill confidence in terms of traceability. High-quality bolts come with comprehensive documentation that traces their origins, materials, and manufacturing history. This traceability ensures accountability and offers peace of mind to end-users, reinforcing trust in their performance and reliability.
In conclusion, the pursuit of bolt quality is a multifaceted endeavor that combines material science, precision engineering, rigorous testing, and innovative design. By focusing on these elements, manufacturers can produce bolts that not only meet but exceed industry expectations, thereby establishing themselves as leaders in the field. Whether in aerospace, automotive, or construction, quality bolts are indispensable, providing the unseen strength and reliability upon which these industries stand. As technology advances, so too will the standards of bolt quality, driven by a relentless pursuit of excellence and safety.