Chemical anchor bolts have become a cornerstone in construction and engineering, differentiating themselves from traditional anchoring systems through their unique chemical bonding process. These anchors excel in applications that demand high load capacities and reliability, particularly in concrete and masonry settings.
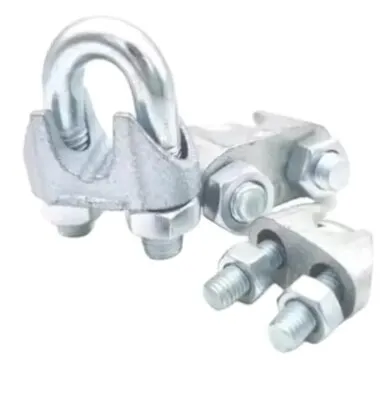
Unlike mechanical anchor bolts that rely on expansion to grip the base material, chemical anchors employ a special adhesive or resin to secure the bolt. This creates a bond at the molecular level, offering unmatched load distribution and strength, making them ideal for high-stress environments and seismic applications. The real strength of chemical anchoring lies in the chemistry — once cured, the resin forms an immovable bond between the fastener and the substrate, even under extreme conditions.
Professional engineers and construction experts recommend chemical anchor bolts for their versatility across a range of applications, from securing heavy industrial equipment to reinforcing structural steel and even in residential construction for retrofitting and seismic upgrades. Their ability to resist dynamic loads and vibrations makes them indispensable in critical infrastructure projects.
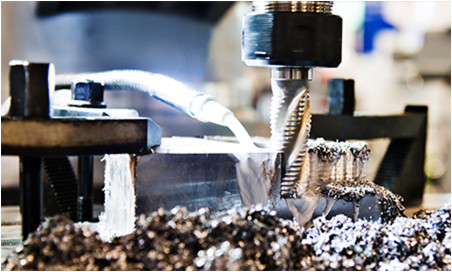
The installation process of chemical anchor bolts underscores their reliability. It starts with drilling a hole in the base material followed by the injection of a precisely mixed resin. The bolt is then inserted, and as the resin cures, it expands, creating a void-free bond that conforms perfectly to the drilled hole. This ensures no movement within the substrate, offering a steadier and more predictable hold compared to mechanical anchors which may loosen over time due to vibrations or material settlement.
Expertise in using chemical anchor bolts is crucial for ensuring optimal performance. Professionals must consider factors such as the type of resin used, the temperature at the time of installation, and the load specifications of the project. Epoxy-based resins are popular for their superior bonding strength and versatility across different conditions, although polyester-based resins are also used for lighter and less critical applications.
chemical anchor bolt
The selection of the right chemical anchor bolt system is essential. Brands like Hilti and Fischer have set the industry standard with systems that provide consistent results and long-lasting reliability. Each system typically comes with a tailored range of components, including resins, dispensers, and setting tools designed to work seamlessly together, ensuring that installations are not just strong but also efficient.
When considering chemical anchor bolts, trustworthiness is reaffirmed by rigorous testing and certifications. These anchoring solutions must comply with stringent international standards, like the European Technical Approval (ETA) and the International Code Council Evaluation Service (ICC-ES) approvals. Such certifications ensure that the products have been tested under various conditions for assurance against failure.
The authority of chemical anchor bolts extends not only from their mechanical properties but also from the endorsements by structural engineers globally.
When installing these anchors, precision and adherence to manufacturer guidelines cannot be overemphasized. Proper installation involves adequate cleaning of the drilled hole to prevent debris from compromising the bond, and the use of tools that ensure correct mixing ratios of the chemical components.
In summary, chemical anchor bolts combine innovative technology with practical functionality, offering unparalleled performance where traditional systems may fall short. Recognized for their adaptability across diverse environments, their use ensures both safety and longevity, positioning them as an essential component in modern construction and engineering projects. With continuous developments in chemical technologies and adhesive sciences, these anchors not only meet but exceed the growing demands for safety and reliability in the industry.