Custom bolts stand as a vital component in manufacturing and engineering, offering tailored solutions to meet the specific needs of different industries. Whether in automotive, construction, or aerospace, these specialized fasteners provide unparalleled advantages in terms of performance, reliability, and efficiency. Throughout the journey of custom bolt manufacturing, there are several key aspects to be explored, including material selection, engineering precision, and the latest advances in production technology. As an expert in this domain, I provide insights based on extensive experience and deep industry knowledge.
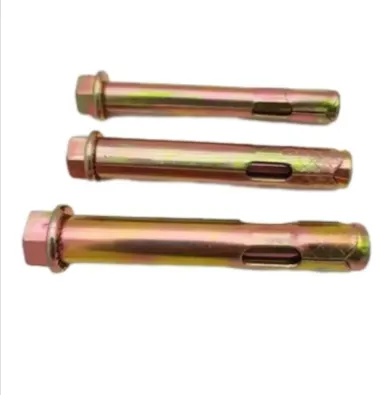
Custom bolts serve as a testament to innovation, as they are designed to adhere to the precise dimensions and tolerances required for specialized applications. Unlike standard bolts, which may not perfectly fit or meet the demands of high-stakes operations, custom bolts are developed with particular specifications in mind, ensuring optimal performance. In critical environments, such as high-pressure systems or extreme temperatures, the right bolt can prevent failures that could lead to costly downtime or catastrophic outcomes.
The journey to create a custom bolt begins with material selection. Various factors, such as tensile strength, environmental resistance, and weight, influence the choice of material. Stainless steel is often preferred for its durability and resistance to corrosion, while titanium may be chosen for its strength-to-weight ratio, crucial in sectors like aerospace. In other instances, alloys can be engineered to achieve specific properties that standard materials cannot offer, providing unique solutions tailored to technical challenges.
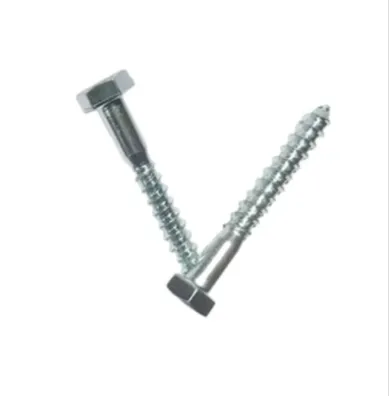
Once material selection is finalized, precision engineering steps in to ensure each bolt meets exact specifications. This process often employs advanced computer-aided design (CAD) software, allowing engineers to model bolts with high accuracy before production. These digital renderings help identify potential issues in the design phase and allow for adjustments that guarantee flawless functionality in real-world applications. Incorporating precision machining technologies like CNC (Computer Numerical Control) further ensures that the dimensions are meticulously followed, down to the micrometer.
Advancements in production technology have revolutionized the manufacturing of custom bolts. Additive manufacturing, commonly known as 3D printing, is now being utilized to create complex bolt designs that were previously impossible or economically unfeasible. This technology not only enhances the ability to prototype and test designs rapidly but also reduces material wastage. Moreover, modern quality control systems, including non-destructive testing methods, ensure that each bolt functions correctly and meets industry standards, further solidifying trust in these components.
custom bolts
In terms of authoritativeness and trustworthiness, manufacturers who specialize in custom bolts often hold industry certifications that attest to their quality and commitment to excellence. Standards such as ISO 9001 for quality management systems or AS9100 for aerospace components underline a manufacturer's capability to produce reliable, high-quality products. Through rigorous testing and adherence to these standards, custom bolt producers instill confidence in customers, establishing themselves as reputable providers.
Moreover, customer feedback plays a pivotal role in continuously improving the design and performance of custom bolts. Experienced manufacturers will often collaborate closely with their clientele, gaining insights and adapting to ensure that the end product not only meets but exceeds expectations. This partnership approach contributes to a product that is highly trusted across industries, as real-world experience and adjustment are fed back into the development cycle, enhancing each subsequent iteration.
Trustworthiness in this sector is also fostered by transparent communication and detailed documentation. Providing clients with comprehensive reports outlining material compositions, performance test results, and compliance with relevant standards creates an open and informative atmosphere. This transparency assures customers of the integrity of the product they are investing in, reinforcing confidence in its application even in the most demanding environments.
In conclusion, custom bolts exemplify the intersection of precision engineering, innovative material science, and cutting-edge manufacturing technologies. By understanding the intricate requirements of each application and adhering to strict quality standards, manufacturers of custom bolts provide solutions that are not only effective but are also based on expertise and reliability. In a world where precision and performance are paramount, custom bolts remain an indispensable component in achieving engineering excellence.