The engineering and construction industries have witnessed significant advances over the years, but one technique that has stood the test of time is cutting bolt threads. Its importance cannot be overstated as it plays a vital role in ensuring the structural integrity and functionality of countless applications. This guide provides an authoritative and in-depth exploration of the process involved in cutting bolt threads, infused with practical experience and expertise.
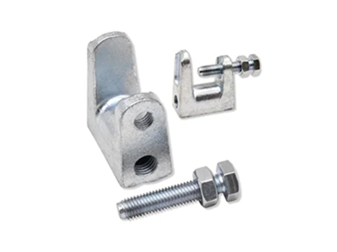
Cutting bolt threads involves creating grooves on the cylindrical surface of a bolt to enable it to fit into a nut or another threaded component. This process is not just about functionality but also about precision and durability. One ensures that the threads are cut to meet exact specifications and tolerances, thus reinforcing trust in the joint's capability to withstand tensions and shear forces effectively.
To start with, the choice of material is paramount. The most common materials used for bolts include stainless steel, carbon steel, and alloys. Each material has unique properties affecting the cutting process. For instance, stainless steel is renowned for its corrosion resistance but is often more challenging to cut due to its hardness. Utilizing high-speed steel (HSS) or carbide cutting tools can significantly aid in achieving cleaner cuts with such materials. In this domain, the use of appropriate lubricants cannot be overlooked. Lubricants reduce friction and heat, which could otherwise lead to thread distortions or tool wear.
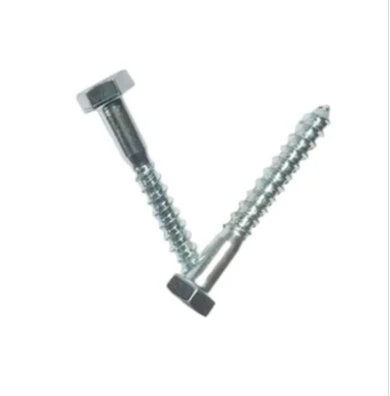
Accuracy and precision in thread cutting demand using machines like lathes or thread cutting machines. The choice between manual and CNC machines can impact the efficiency and consistency of the threads. While manual machines might be ideal for bespoke or smaller volumes, CNC machines provide unmatched precision and speed, crucial for larger production runs.
A critical aspect of thread cutting is adhering to internationally recognized standards such as the Unified Thread Standard (UTS) or the ISO metric screw thread standards. These standards ensure compatibility and interoperability between components fitted worldwide. Any deviation from these standards could lead to mismatched pairs, potentially compromising structural integrity.
cutting bolt threads
Our experience with various threading techniques such as single-point threading, die cutting, and rolling offers insights into their unique advantages and potential downsides. Single-point threading, typically done on a lathe, is ideal for large diameter threads where precision is critical. Die cutting is suitable for smaller threads and is relatively quicker but may not offer the same precision level. Thread rolling, on the other hand, involves cold forming of threads through pressure. While not a cutting operation per se, it results in stronger threads with superior surface finishes, making it an attractive option for high-strength applications.
Another critical factor influencing thread cutting is the pitch and diameter of the threads. These elements define the profile and depth of the cut, directly affecting the bolt's performance under load. Thread gauges are tools of choice for ensuring that pitch and diameter align with requisite standards, thus maintaining a thread's integrity.
Safety, often overlooked, is paramount when cutting bolt threads. Protective eyewear, gloves, and appropriate clothing protect operators from metal shavings and splinters. Furthermore, ensuring that machines are well maintained and operators are well trained minimizes the risk of accidents and improves the quality of thread production.
Trustworthiness in this craft is built over years of practice and adherence to stringent standards. Certified processes not only guarantee a higher quality of work but also earn the trust of clients and partners. Our legacy speaks volumes about our commitment to excellence in thread cutting, reinforcing the bonds of reliability and credibility with every bolt produced.
In conclusion, cutting bolt threads is more than just a mechanical process; it is a critical engineering task that requires attention to detail, precision, and expertise. With advancements in technology and techniques, the future of thread cutting looks promising, promising added efficiency, quality, and safety improvements. Whether you are a seasoned professional or a novice, understanding these nuances will empower you to produce bolts that are not only functional but also exemplary in performance and reliability.