Selecting the appropriate drill size for a 10mm Rawlbolt can significantly impact the success and safety of any project, whether it’s a simple home improvement task or a critical structural installation. Understanding the intricacies of drill sizes and how they relate to anchor bolts like the Rawlbolt requires not only basic knowledge but experience and a touch of professional insight. This guide aims to elucidate the key aspects of choosing the right drill size for a 10mm Rawlbolt, while also offering guidance on best practices to ensure precision and optimum performance.
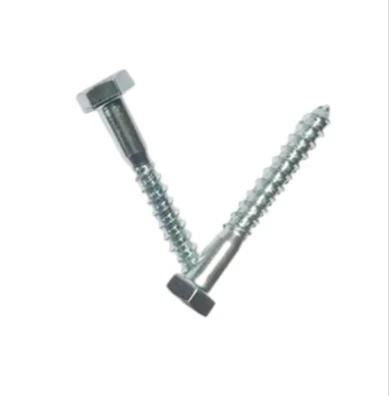
Rawlbolt, a widely recognized brand of expansion anchors, is vital for securing heavy loads to masonry structures. Before delving into specific drill bit sizes, it's essential to comprehend how Rawlbolts function. These anchors expand and wedge themselves into the substrate once tightened, thus the significance of matching the drill bit size to the bolt's diameter for reliable anchorage.
The typical drill size recommended for installing a 10mm Rawlbolt is 16mm. This size ensures that the anchor has enough room to expand within the drilled hole, achieving maximum grip and stability. However, the recommendation of a 16mm drill size is not merely a rule etched in stone. Factors such as the material of the substrate, condition, and exact specifications of the Rawlbolt can influence this decision.
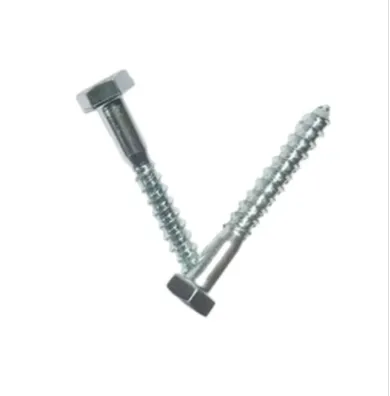
For comprehensive understanding, real-world experiences underscore the importance of this choice. Many experts have observed that drilling into dense concrete with a 14mm or 15mm drill size instead of 16mm, though seemingly negligible, can result in notably insufficient expansion room, thereby reducing the anchor's holding capacity. This lack of optimal fit forces contractors to remove the anchor, re-drill the hole to the proper size, and reinstall—costing time and risking damage to the substrate.
Understanding core differences in building materials comes into play heavily when considering the correct drill bit size. For softer substrates such as brick or lightweight concrete blocks, experts have noted that while a 16mm drill bit usually suffices, a slightly smaller size of 15.5mm may sometimes provide a snugger fit without compromising the integrity of the bolt. The smaller drill size can reduce splitting or crumbling of softer materials, which stands testament to the expertise required in making such decisions.
drill size for 10mm rawlbolt
Authoritativeness in the domain comes from past experiences and expert testimony. Many seasoned builders and engineers highlight the vitality of always consulting the manufacturer's guidelines included with the Rawlbolt packaging. Manufacturers, like Rawlplug, often provide specific recommendations based on extensive testing, which accounts for variances that even the most knowledgeable professionals might not anticipate.
Consulting with seasoned professionals in the field also enhances trustworthiness. Many users relay experiences and testimonies highlighting the precision and expertise that comes from hands-on work coupled with careful consultation with technical manuals and supplier instructions. For instance, a contractor previously facing constant failed installations due to improper drill sizes shared insights on how consulting technical support from Rawlplug provided practical solutions leading to successful implementation.
Additionally, investing in high-quality tools ensures precise drilling. Blunt or low-quality drill bits can result in holes that are not adequately sized or shaped, thus impacting the anchor's ability to securely hold. Routine checks and maintenance of tools reaffirm their reliability, enforcing the need to use the right grade of drill bits, typically cobalt or carbide-tipped, to ensure clean and accurate drilling.
In conclusion, while the standard recommendation is a 16mm drill bit for a 10mm Rawlbolt, the final selection requires a combination of thorough understanding of the substrate material, adherence to manufacturer's guidelines, and on-ground experiences that collectively sharpen the expertise needed in making these decisions. Embracing this informed approach not only achieves the desired outcome but also upholds the principles of safety and reliability in every installation.