The intricate world of manufacturing nuts and bolts is a domain steeped in expertise and precision. As fundamental components of countless mechanical assemblies, their production process requires a blend of advanced technology, deep knowledge, and skilled craftsmanship to ensure quality and reliability.
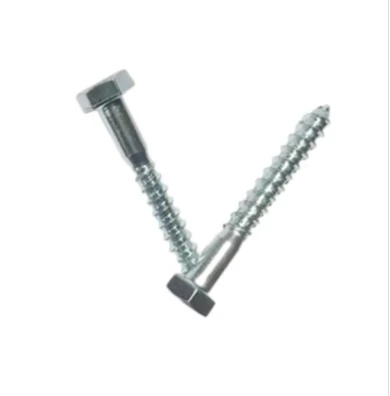
Understanding the process begins with the selection of raw materials. High-grade steel is typically the material of choice due to its exceptional durability and strength. The journey from raw steel to finished product commences in a steel mill where the material is transformed into appropriate sizes, often in wire or rod form, ready to be shaped into nuts and bolts.
Once the raw material is prepared, the forming process begins. This is a key stage, where cold forging or hot forging methods are employed depending on the specific requirements of the product. Cold forging is executed without the need for heating the material and is favored for its ability to create stronger threads. In contrast, hot forging involves heating the metal to make it more malleable for shaping when intricate designs are needed.
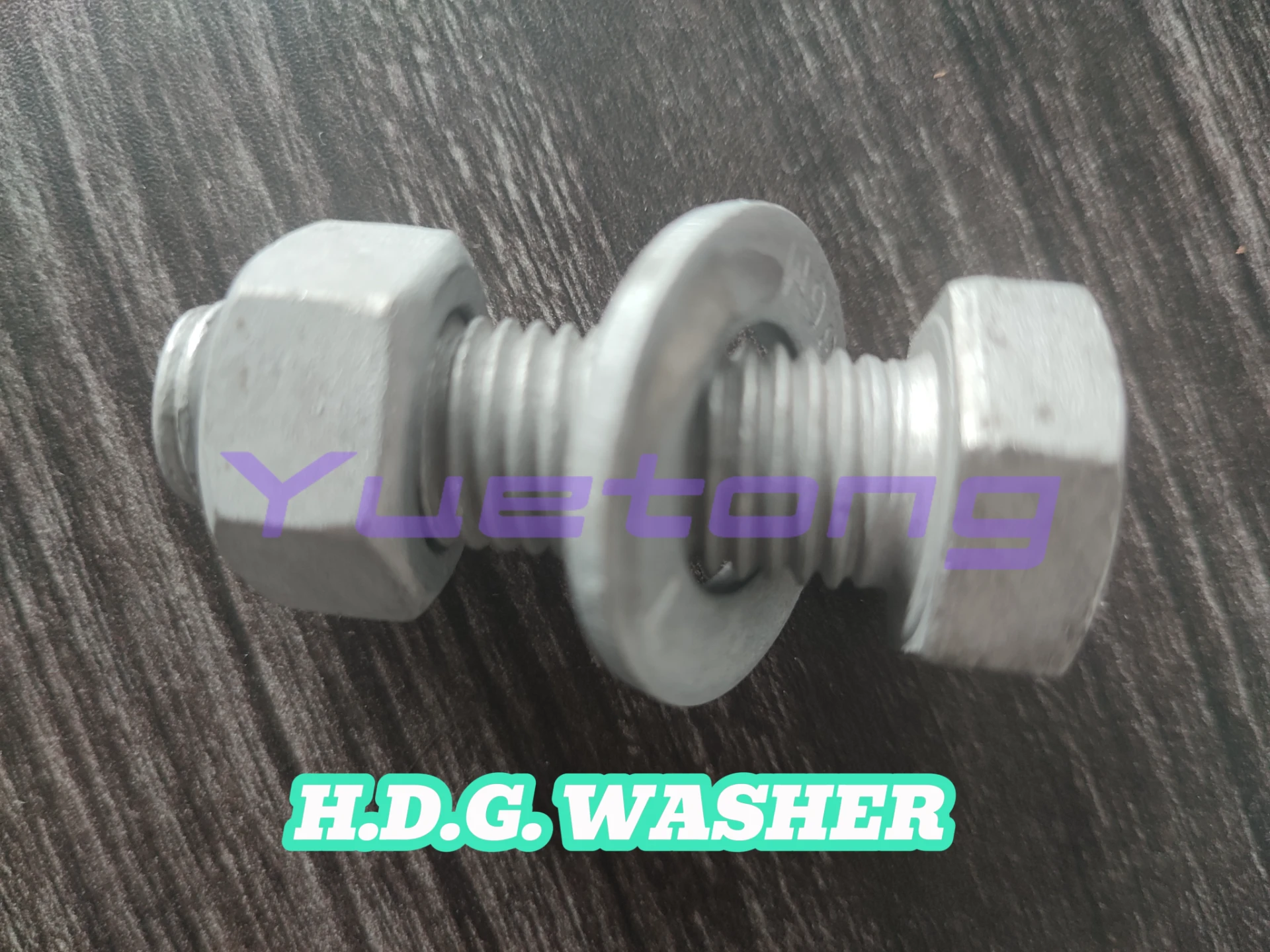
The next critical stage is threading, a process that requires precision and expertise. Threading in bolts is achieved by rolling, a preferred technique over cutting due to its ability to produce stronger, more reliable threads. For nuts, threading is done by tapping, where an internal thread is cut into the pre-shaped nut. The tolerance between the nut and the bolt must be meticulously controlled to ensure a precise fit, which is fundamental in delivering consistent performance in applications.
Heat treatment follows, a specialized process that enhances the mechanical properties of the nuts and bolts. This involves heating the materials to a specified temperature and then cooling them in a controlled environment. The result is a product with increased strength and resistance to wear and fatigue, extending the lifetime of the assemblies in which they are used.
process of making nuts and bolts
Surface finishing is equally integral to this manufacturing process. By applying coatings or platings such as zinc or chrome, manufacturers not only improve corrosion resistance but also contribute to the final product’s aesthetic appeal. The choice of finish is determined by the operational environment the nuts and bolts are expected to encounter.
Quality control is an uncompromising element of the production line. Each batch of nuts and bolts is subjected to stringent testing protocols, ensuring adherence to industry standards. Dimensional accuracy, tensile strength, and thread integrity are quantitatively assessed to confirm that the products meet both consumer and regulatory expectations.
Moreover, ongoing innovations in the field are pushing the boundaries of what's possible in nut and bolt manufacturing. The introduction of smart manufacturing techniques, such as computer numerical control (CNC) threading machines and automated quality inspection systems using AI, heralds a new era of precision and efficiency. These advancements not only streamline the production process but also reduce human error, leading to even higher levels of quality consistency.
A mastery of the nuts and bolts production process involves more than technical prowess; it requires a commitment to quality and a proactive embrace of emerging technologies. Leading manufacturers continuously refine their methods, drawing on decades of experience and engineering advancements to create products that meet the increasingly demanding requirements of modern industries.
In summation, the production of nuts and bolts is a sophisticated interplay of material science, engineering expertise, and advanced manufacturing techniques. This dynamic process is driven by a combination of traditional methods honed over years and cutting-edge technology, ensuring each nut and bolt produced is a testament to their critical role in the fabric of industrial and construction applications worldwide. Such meticulous manufacturing practices provide assurance in the performance, safety, and longevity of the vast array of structures and machines they help hold together.