Threaded fasteners play a critical role in the vast realm of industries and home improvement projects, providing a pivotal means of holding materials together. With my extensive experience in fastening technology, I've come to appreciate the varied types of threaded fasteners, each designed to meet specific requirements and standards. This exploration delves into the different types of threaded fasteners, elucidating their uses and benefits.
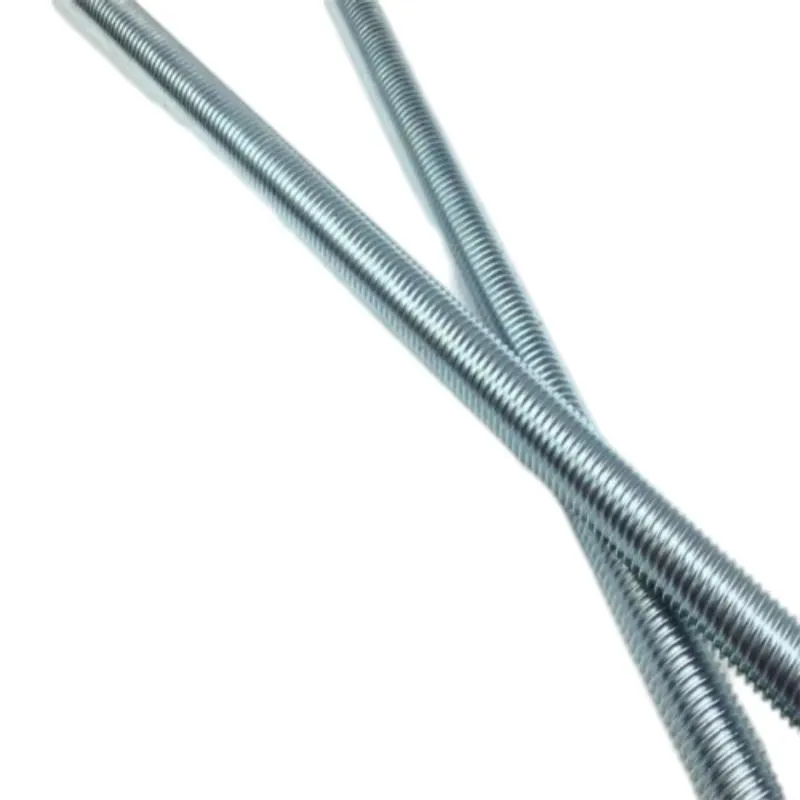
In the world of threaded fasteners, screws are one of the most commonly used, known for their versatility and strength. Among screws, wood screws are prevalent in carpentry and woodworking. They are specifically designed to carve their own thread into the wood, ensuring a tight and durable grip. These screws usually feature a tapered shank and a sharp point that easily penetrates the wooden surface.
Machine screws, on the other hand, are employed in machinery and metalworks. They are used with nuts or tapped holes,
offering precise and robust fastening. A distinct feature of machine screws is their uniform diameter, with threads cut along the entire length. This design allows for a consistent and secure connection in metals and plastic components.
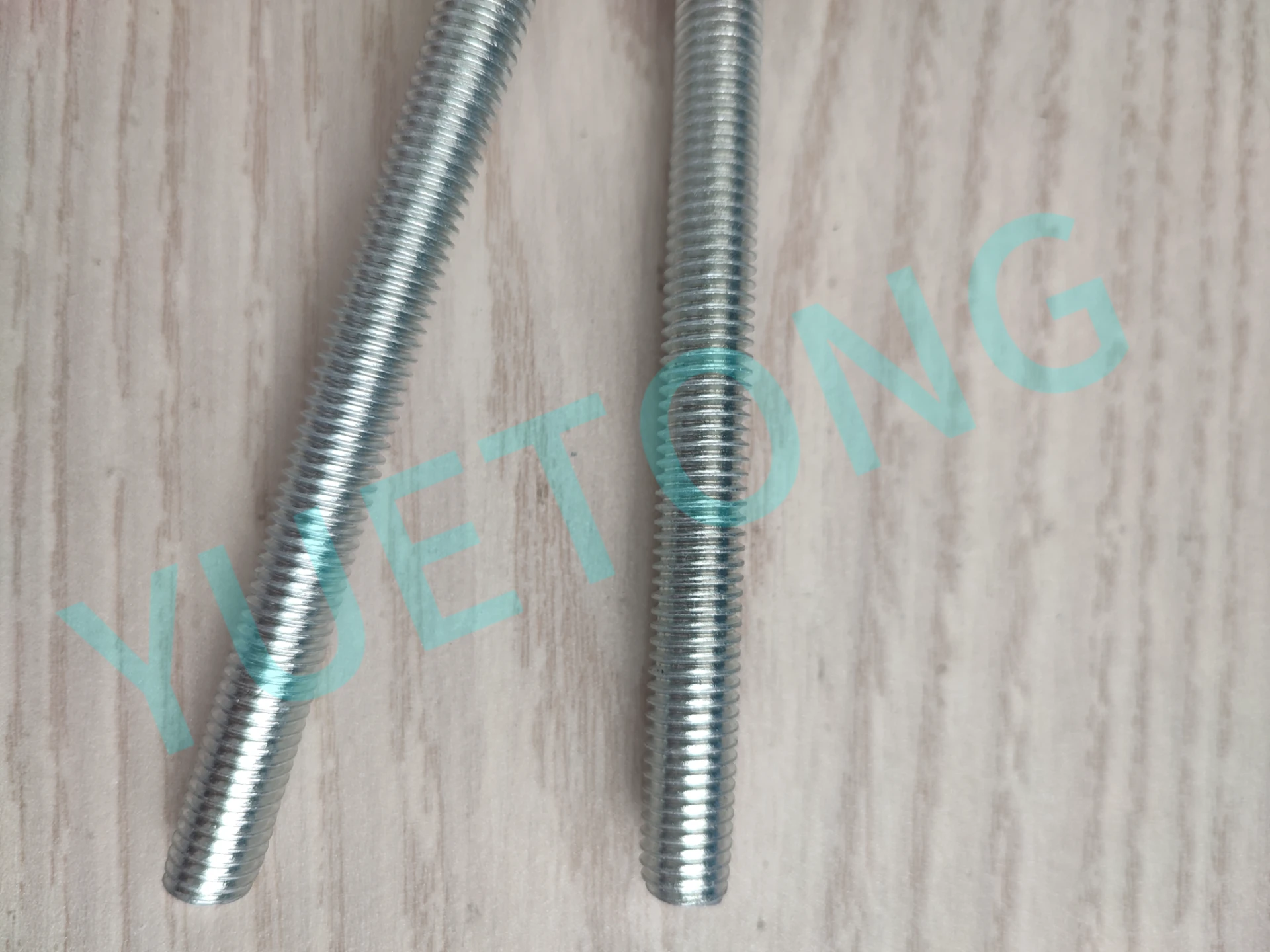
For heavy-duty applications, structural bolts stand out due to their impressive tensile strength. These are primarily used in the construction of buildings and infrastructure, including bridges and towers. Made from high-grade steel, structural bolts can withstand immense loads and environmental stressors, making them indispensable in construction industries.
Another prominent threaded fastener is the carriage bolt, characterized by its rounded head and square neck that prevents rotation as the nut is tightened. Carriage bolts are commonly used in wood-to-wood or wood-to-metal applications, where a smooth, domed head is required on one side to prevent snagging or injuries, such as in playground equipment and furniture.
In plumbing and electronic applications, hex bolts are prevalent due to their easy-to-grip six-sided head, which simplifies installation in tight or awkward spaces. These bolts are often available in a range of materials, including stainless steel and brass, catering to various requirements regarding corrosion resistance and conductivity.
types of threaded fasteners
Threaded rods, often used as a versatile fastener, provide an all-thread solution suitable for tension or compression loads. They're frequently employed in construction, automotive, and electrical industries for temporary or permanent joinery. Threaded rods offer the advantage of adjustable length and are often used in situations where the length needs to be customized on-site.
Specialized screws, such as drywall screws, have emerged for specific tasks. With their fine threads and sharp points, drywall screws provide excellent holding power in drywall applications without damaging the plaster. Their drywall-specific design reduces the risk of damaging the board, maintaining structural integrity and aesthetics.
When seeking anti-loosening properties, the lock nut is a go-to option. Lock nuts come in various designs, including nylon insert lock nuts and metal lock nuts. These specialized nuts resist vibrations and prevent the components from coming apart, a crucial feature in automotive and aerospace industries where safety is non-negotiable.
U-bolts deserve mention for their unique U-shape, designed to secure pipes, cables, and other cylindrical objects. Available in various sizes and materials, U-bolts provide a firm grip and are often used in piping systems, vehicle suspension, and as anchor bolts, illustrating their versatility across diverse sectors.
For high-precision assemblies, such as electronics, set screws offer an inconspicuous yet effective fastening solution. Designed to secure an object within or against another object without the need for nuts, set screws are utilized in pulleys, gears, and other rotating devices.
Understanding the strengths and appropriate applications of each type of threaded fastener is essential for maximizing performance and reliability. Professionals across industries should consider material compatibility, environmental conditions, and mechanical stress when selecting a fastener type. Precision in choice and application of these components does not only ensure the success of the current task but also prevents future mechanical failures, fostering trust in products and structures built to last.