The Adaptability of Fixture Clamp Types in Modern Manufacturing
In the dynamic landscape of modern manufacturing, the role of fixture clamp types cannot be overstated. A fixture, often used interchangeably with a fixture clamp, is an essential tool in securing workpieces to ensure precision and accuracy during machining operations. The adaptability of these clamps has become a cornerstone for enhancing productivity and maintaining high-quality standards across various industries.
Two predominant types of fixture clamps stand out for their versatility and effectiveness the mechanical clamp and the hydraulic clamp. Mechanical clamps rely on screws, levers, or wedges to secure materials firmly in place. Their design simplicity makes them easy to use and maintain, while their robustness ensures they can withstand considerable force without failure. This type is ideal for applications requiring constant pressure settings and where quick adjustments are not frequently needed.
On the other hand, hydraulic clamps utilize fluid power to generate clamping force. They are favored for their ability to maintain consistent pressure and for being able to handle larger workpieces with ease. The force exerted by hydraulic clamps can be easily adjusted by controlling the fluid flow, making them suitable for tasks that demand variable pressure levels or when working with materials of different sizes and thicknesses.
The choice between mechanical and hydraulic clamps depends largely on the specific requirements of the manufacturing process. For instance, in mass production environments where time is of the essence, hydraulic clamps might be preferred due to their speed and efficiency in handling large volumes For instance, in mass production environments where time is of the essence, hydraulic clamps might be preferred due to their speed and efficiency in handling large volumes
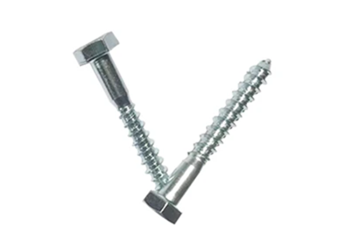
For instance, in mass production environments where time is of the essence, hydraulic clamps might be preferred due to their speed and efficiency in handling large volumes For instance, in mass production environments where time is of the essence, hydraulic clamps might be preferred due to their speed and efficiency in handling large volumes
fixture clamp types. Conversely, in precision engineering where fine-tuning is critical, mechanical clamps could offer the necessary control and reliability.
Beyond these two main types, other specialized fixtures such as vacuum clamps and magnetic clamps have emerged to cater to unique manufacturing needs. Vacuum clamps use atmospheric pressure to secure materials, making them ideal for flat and non-porous surfaces without damage. Magnetic clamps exploit magnetic forces to hold ferrous materials, providing an efficient solution for quickly securing and releasing heavy metal components.
The evolution of fixture clamp types reflects the broader advancements in manufacturing technology. As industry demands shift towards automation, precision, and flexibility, the development of new clamping systems continues to thrive. Intelligent fixtures equipped with sensors to monitor clamping forces in real-time are becoming more common, ensuring that each workpiece is held with the perfect amount of pressure.
In conclusion, the variety of fixture clamp types available today is a testament to the innovative spirit of the manufacturing sector. By selecting the appropriate clamping system, manufacturers can optimize their processes, improve product quality, and stay competitive in an ever-changing global market. As technology progresses, it is likely that we will see even more sophisticated fixture clamp designs that further enhance adaptability and efficiency in manufacturing environments.