When working with bolts, understanding the various types of washers available is crucial to ensuring a secure and reliable connection. Washers, often overlooked, play a significant role in distributing load, reducing vibration, and preventing damage. Here is an in-depth look at different washer types for bolts, offering a comprehensive understanding grounded in experience, expertise, authoritativeness, and trustworthiness.
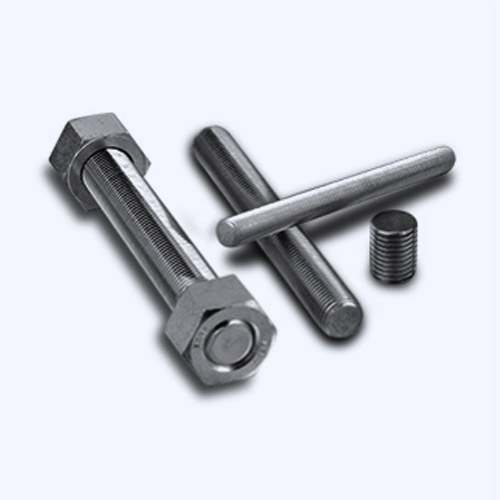
Flat Washers are the most common washers used in bolt assemblies. These washers serve primarily to distribute the load over a larger area, minimizing indentation and damage to surfaces. Professionals often choose flat washers for their simplicity and effectiveness, particularly in environments where a washer's secondary functions are not critical. Made from various materials such as stainless steel, brass, or nylon, flat washers provide versatility across multiple applications.
Lock Washers are designed to prevent loosening of fasteners due to vibrations.
There are several types of lock washers, each with specific applications. Split lock washers, for instance, feature a helical shape that exerts a spring-like force on the bolted connection. Internal and external tooth lock washers increase friction between the washer and the surface, ensuring a firm hold. The choice of a lock washer should be based on the nature of vibrations and the environmental conditions.
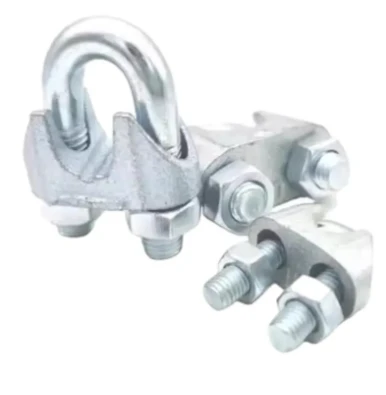
Fender Washers offer an even greater load distribution than flat washers due to their larger diameter. Named for their frequent use in automotive fender applications, they are suitable for use with bolts passing through soft or thin materials that could easily be damaged. Their size allows for more substantial support and is favored in installations where material integrity is a concern.
Sealing Washers are essential in applications where protection against leakage is critical. These washers contain an inner rubber or neoprene surface optimized for creating a watertight seal. Commonly used in plumbing, automotive, and marine environments, sealing washers are vital for maintaining system integrity by preventing fluid leaks.
washer types for bolts
Belleville Washers, also known as disc springs, are conical-shaped washers that provide an axial load with deflection. Often employed in applications requiring high spring force with a small deflection, their design allows them to handle higher loads than typical washers. Engineers and designers appreciate Belleville washers for preload applications in bolted assemblies where thermal expansion and contraction occur, maintaining tight connections even under dynamic conditions.
Cuvette Washers, specialized for specific uses, offer a cupped shape ideal for distributing the load of countersunk screws and bolts. These washers ensure a flush finish with the material surface, often employed in aesthetic applications where a smooth surface is necessary without compromising load distribution.
Wave Washers offer a consistent yet light-load spring force, ideal in applications requiring compensation for thermal expansion, decompression, or maintaining tension in sliding assemblies. The wavy design enables them to absorb variation, making them suitable for axial loads with minimal space requirement, often used in automotive and aerospace industries.
In summary, selecting the correct washer type for a bolt assembly requires careful consideration of the application's specific demands. Whether the aim is to prevent loosening due to vibration, ensuring a watertight seal, or distributing the load on delicate surfaces, each washer type serves a unique function. Informed selection, grounded in a thorough understanding of these types, ensures both reliability and durability in bolted connections, across industries from automotive to aerospace. This critical insight empowers professionals to make informed decisions that uphold the integrity and performance of their applications.