Navigating the complex world of bolt manufacturing reveals a fascinating blend of science and artistry. Mastery over this intricate process requires a profound understanding of the materials, methodologies, and machinery that confer strength and reliability to the bolts vital to countless applications. The journey from raw material to finished product is a testament to human ingenuity and engineering prowess.
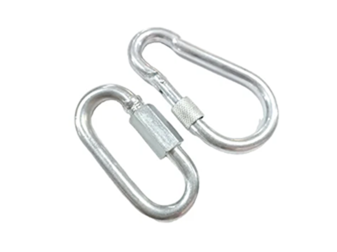
Bolts are fundamental components in various constructions and machineries, yet their significance is often understated. The precision in their manufacturing, however, underpins the safety and durability of entire structures. This intricacies-demanding industry pivots around key factors like the choice of material, the specifics of the manufacturing process, and adherence to rigorous quality standards.
The journey begins with raw materials, usually steel, due to its remarkable strength and resilience. The selection of material is crucial, as it significantly impacts the performance of the final product. Experts employ advanced metallurgical techniques to tailor the properties of the steel, ensuring it meets the rigorous demands placed on bolts in service.
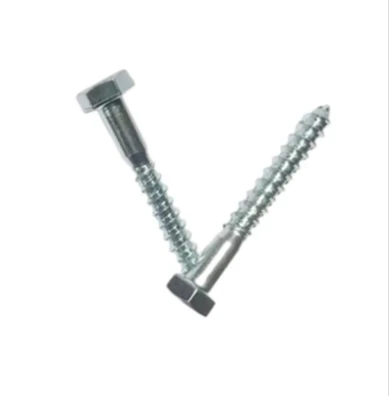
The initial step in the manufacturing process is wire drawing. A large coil of steel wire is drawn through a series of dies to reduce its diameter. Precision at this stage is paramount, as any deviation can affect the bolt's strength and thread quality. Experienced operators use calibrated dies and roller mechanisms to ensure uniform wire diameter, setting the stage for subsequent processes.
Once the wire is prepared, the cold forging process commences. This technique involves shaping the bolt without heating the material, preserving the steel’s tensile strength. Cold forging requires sophisticated machinery and skilled operators to produce bolts with intricate dimensions and tight tolerances. Modern forging machines are equipped with computerized controls that offer unmatched precision, producing bolts that fit perfectly into their designated applications.
bolt manufacturing process
Thread rolling is the subsequent step, and it exemplifies the fusion of technology and craftsmanship. Unlike cutting threads, rolling forms them by pressing and rolling the blank bolt between two dies. This process enhances the threads' strength and fatigue resistance, attributes critical to the bolt's performance in mechanical assemblies. The expertise involved in setting up the thread rolling machines is crucial for quality output, demanding practiced eyes and technical acumen.
Finally, quality control is woven throughout the manufacturing journey, not just as a concluding step. Sophisticated inspection technologies such as laser scanning and ultrasonic testing play pivotal roles in ensuring each bolt meets stringent specifications. The commitment to quality is a hallmark of excellence in bolt manufacturing, reflecting a dedication to safety, reliability, and performance.
It’s through the intersection of expertise and technology that bolt manufacturing achieves its remarkable efficiencies and precision. The process from wire to finished bolt is orchestrated by industry professionals whose knowledge and experience shape the performance and safety of modern machinery and structures. By maintaining these high standards, manufacturers assure the industry of bolts that not only meet but often exceed, the expectations of their demanding roles in infrastructure and technology.
The role of bolt manufacturing in modern industry is nothing short of foundational. Understanding the nuances of this process highlights the industry’s commitment to excellence and innovation, rooted in expertise and a continuous pursuit of improvement. The unyielding dedication to quality control and advancement of manufacturing techniques ensures that bolts remain steadfast in their role as the unseen backbone of engineering and architecture. This meticulous level of detail and craftsmanship secures the industry's reputation for trustworthiness and authority, embodying the pinnacle of engineering achievement.